彩色光阻剂开发历史
彩色光阻剂发展史
我们公司于 1983 年首次开始开发彩色光阻剂。最初开发的是正型聚酰亚胺抗蚀剂,自1990年应用于液晶面板等产品的量产线以来,我们主导了主流负型抗蚀剂的开发。
图1彩色光阻剂发展史
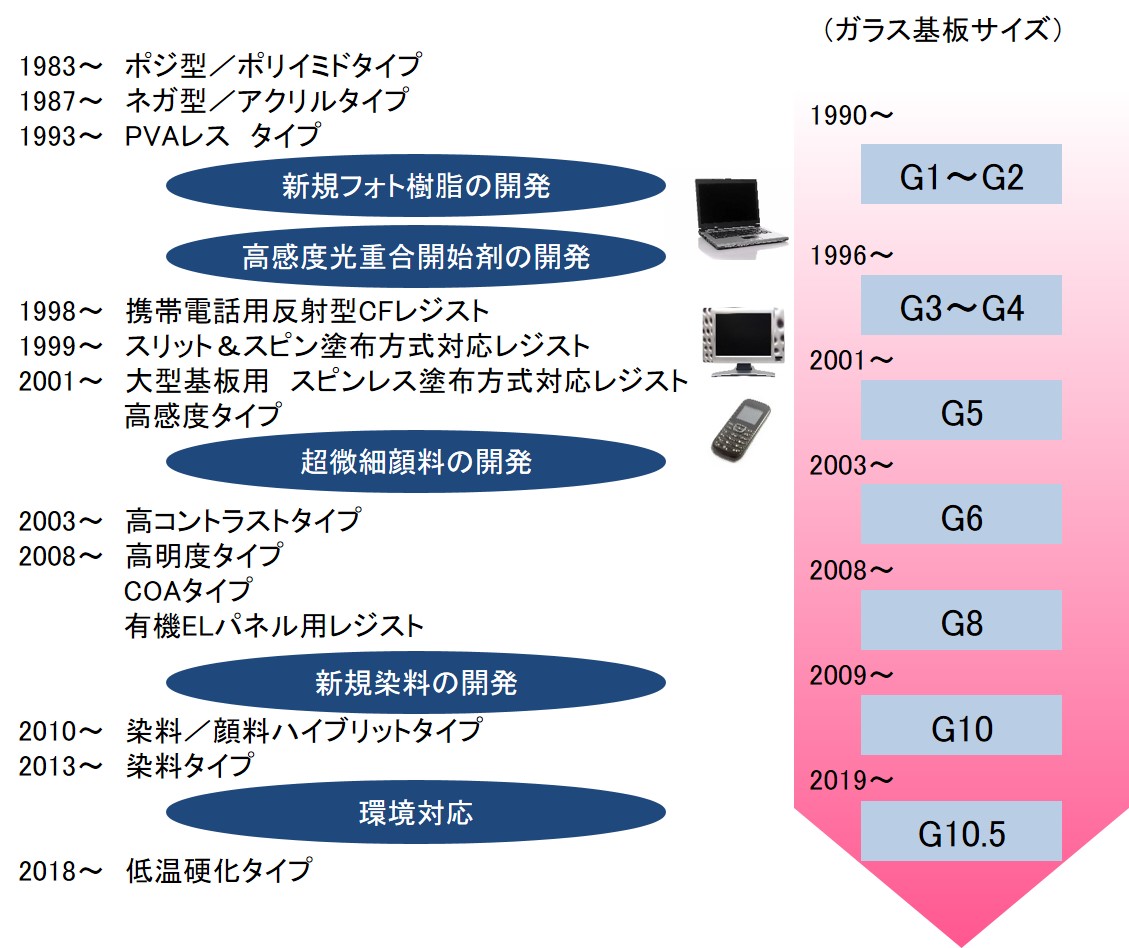
1990 年代,大型电视的需求增加,液晶面板制造商每一代都致力于增加玻璃基板 (G) 的尺寸。在这样的开发竞争中,为了提高液晶的良率(良品率)和降低成本,更大的玻璃基板更具优势。因此,随着玻璃基板的大型化,我公司努力提高彩色光阻剂所需的性能(涂膜、感光度、镀膜工艺)。从2001年在台湾推出G5开始,我们现在还提供G10.5大型基板的产品,为提高液晶面板的量产性能做出了贡献。此外,为了提高产品功能,我们还开发了高对比度、高亮度和染料型抗蚀剂。我们一直负责各种平板显示器的着色。
图2玻璃基板尺寸的变迁
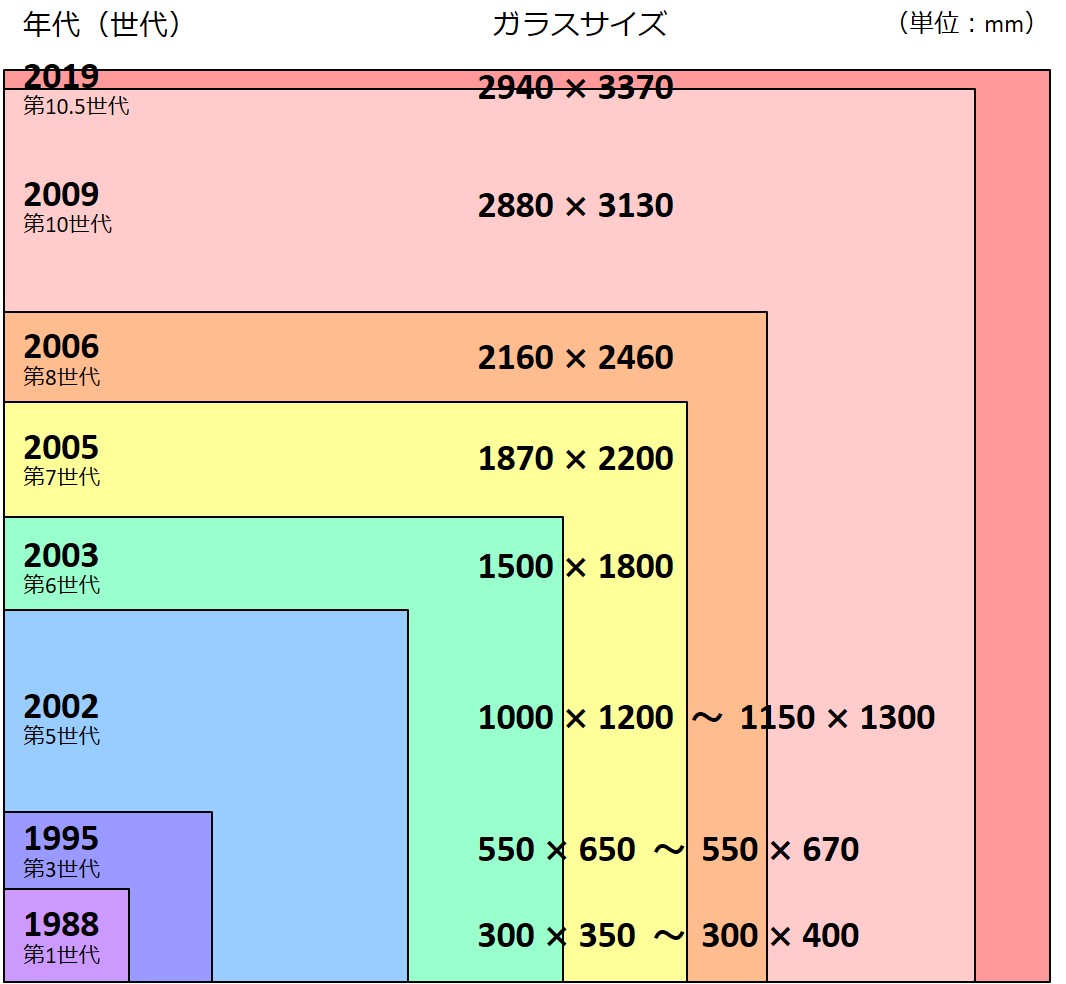
彩色光阻剂发展背后的秘密故事
大约在 1988 年,我们公司开始将制造彩色光阻剂作为一项严肃的业务。最初的开发始于 20 世纪 80 年代初,当时一位客户联系我们共同开发彩色光阻剂。此后,研究在东京板桥区工厂的一角悄悄进行,直到2000年建立了森山工厂,以适应液晶电视和IT设备产量的增加。研究所里聚集了一名老员工和两名新人。
项目开始时,只有一个人了解彩色滤光片,因此开发工作是在摸索中进行的。当时,彩色滤光片的制造方法仍在开发中,除了目前主流的颜料光刻胶方法外,还考虑了染色、PI 刻蚀、电沉积和印刷等制造方法。最初,与染色法相比,颜料抗蚀剂法的彩色滤光片对比度明显较低,但这是由于颜料颗粒对光的散射较大。因此,人们创造了一种方法,通过微型化工艺使颜料颗粒更细,从而实现高对比度。
30年前审查 使用的CF制法 |
制法概要 |
---|---|
PI蚀刻法 | 将分散有颜料的聚酰胺酸NMP溶液涂布并干燥,使用正性抗蚀剂形成图案,并通过加热闭合环以形成PI膜。 |
印刷法 | 采用凹版胶印方式进行三色印刷。 |
染色法 | 用三种颜色的染料染色树脂,如图案化的明胶。 |
颜料抗蚀剂法 | 颜料使用丙烯酸负性抗蚀剂与分散有 |
另外,据说仅将彩色光阻剂固定在玻璃基板上就非常困难。在开发初期,为了将其固定在玻璃基板上,我们在抗蚀剂上涂上聚乙烯醇(一种氧气阻挡膜),然后将其暴露在紫外线下并显影以形成图案。然而,应用这种氧气阻隔膜需要大量的时间和成本,因此出现了一个要求:“是否可以省略这个过程?”按照当时的常识,通过将抗蚀剂暴露在空气中来形成图案是不可想象的。无论尝试多少次,曝光都不顺利,当他显影时,抗蚀剂涂层完全消失。然而,经过不断的尝试和错误,我们通过优化光聚合引发剂的类型和用量,成功地固定了涂膜。这项技术在当前彩色滤光片的生产中得到了牢固的继承。
20世纪90年代,随着液晶面板的大型化和产量的增加,彩色光阻剂的产量急剧增加。从1996年到2005年的10年间,企业利润增长了约10倍。 2000年,我们建立了森山工厂,生产彩色光阻剂,该业务已发展成为支撑公司的支柱业务。大约在这个时候,国内电子厂商纷纷开始研发新的液晶电视产品。因此,电视彩色滤光片的规格变得更加严格,每年都有新产品被开发出来。
特别受追捧的是高对比度(明暗之间的差异)。为了实现这一点,需要通过减小颜料颗粒的尺寸来减少光的散射,但另一方面,颗粒越小,它们就越难分散,抗蚀剂就越容易变得不稳定。因此,为了创造更明亮、更生动的画面,我们开始推进分散技术并开发新的颜料,让光线更容易通过。通过反复试验,我们继续开发出可以满足各种复杂需求的彩色光阻剂。
此后,虽然国内液晶电视需求下降,但台湾、韩国和中国等亚洲国家的需求却有所增加。由于大型玻璃基板工厂的不断扩建,制造基地纷纷转移到海外。此外,从减少环境影响的角度来看,用于图像传感器的彩色光阻剂、用于微显示器的彩色光阻剂和低温固化光刻胶的需求不断增长。当彩色光阻剂被安装在智能手机和数码相机等多用途和多功能产品中时,需要进一步提高其功能。
联系我们
东洋翊绚株式会社
TEL:+81-3-3272-3457