Structure of color resist
What is color resist?
Color resist is a kind of colorant based ink used in color filters. It is called color “resist” for its resistance towards chemical and physical applications during the manufacturing process. Color resist is also known as resist ink.
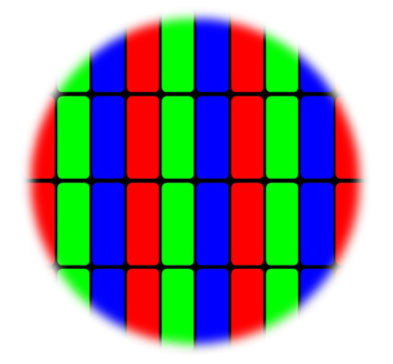
A color filter consists of a glass substrate coated by three types of color resist (RGB; red, green and blue) in a specific pattern. Since each spot of color resist (sub pixel) is very small, it is difficult to color each dot one by one.
Here, the color resist property proves useful. By applying color resist to the entire surface, masking the areas to be removed, and exposing the desired portions to ultraviolet light for curing (insolubilization), it is possible to selectively retain color resist in specific areas after etching with a developing solution. This process allows for obtaining RGB patterns on the glass substrate. (This kind of color resist is called a negative resist.)
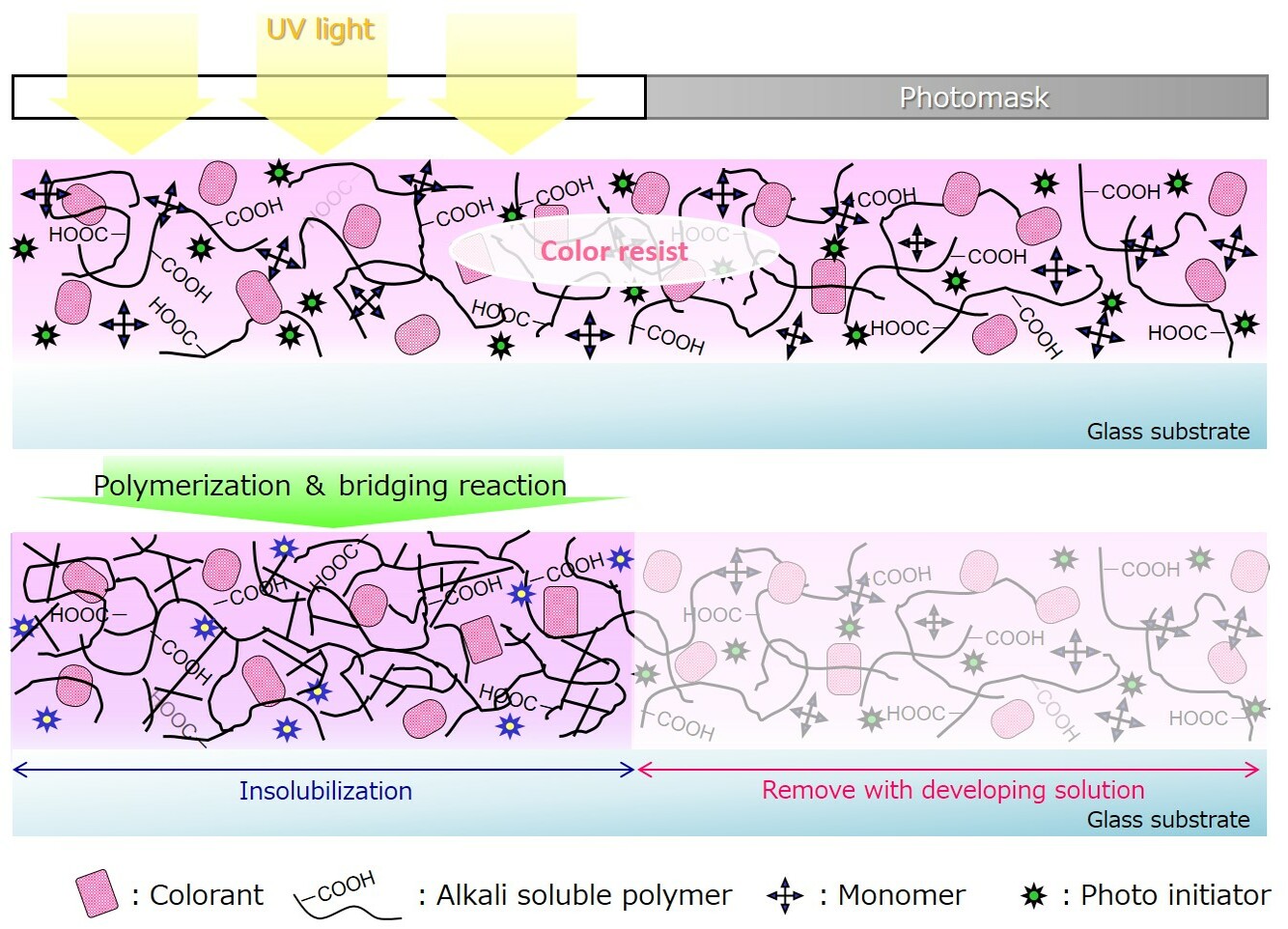
Ingredients of color resist
Color resist is manufactured by mixing the mill base, which consists of colorants, resin and solvent, with a photo initiator and various additives for UV triggered polymerization.
Ingredients of color resist | Functions |
---|---|
Colorant | ■Determines spectroscopic character. Normally, a mixture of two or more colorants (Main colorant & toning colorant) is used. |
Resin | ■Gives dispersion stability when absorbed onto pigment surface. ■Gives adherence towards the glass substrate. ■Gives alkali developability. |
Solvent | ■Adjusts viscosity and dryness. ■Gives coating suitability. |
Monomer | ■Gives insolubility via polymerization and cross-linking (photocurability). |
Photo initiator | ■Initiates polymerization reaction in the UV irradiated area (photocurability). |
Dispersant | ■Gives dispersion stability to colorant. |
Additives | ■Prevents coating defect (leveling agent, etc.) ■Gives preservation stability. |
Our color resist
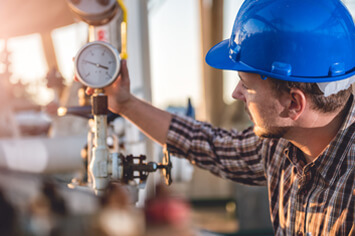
Refinement and dispersion technology of pigments
Color materials for electronics such as FPDs require a high transmission ratio of light. In order to achieve this, the technology to refine the pigment particles at nano-level is essential. With this technology, we are able to adjust the pigment size according to various applications.
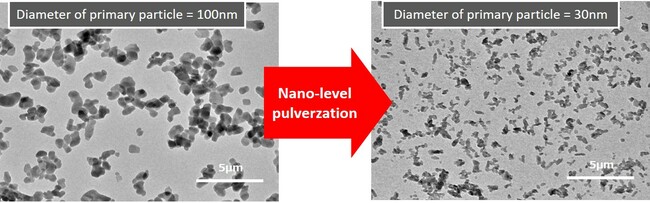
Making pigment particles disperse uniformly is also essential to improve the transmission ratio. By processing the pigment surface, we are able to stabilize the uniformly dispersed state and avoid any precipitation. With this technology, we are able to provide highly functional color materials with good fluidity (which makes it easier to apply to a substrate) and high transmission, suited for use in electronics.
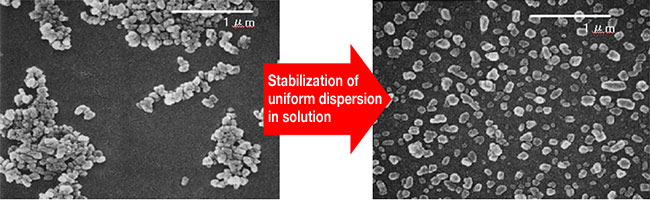
Development of new colorants (OPTLION™ GREEN)
OPTLION™ GREEN is a brand-new colorant developed by our company. Currently, we have 2 types, OPTLION™ GREEN 8880 and OPTLION™ GREEN 8890. By applying them to a color filter, the real beauty of nature can be reproduced more vividly and brightly. In addition, by applying OPTLION™ GREEN, the color gamut will be expanded and enhance the color reproduction performance of the display.
Images using OPTLION™ GREEN
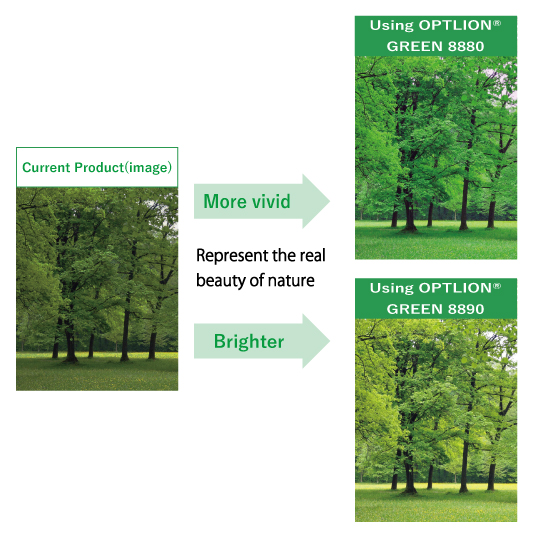
Color gamut of OPTLION™ GREEN
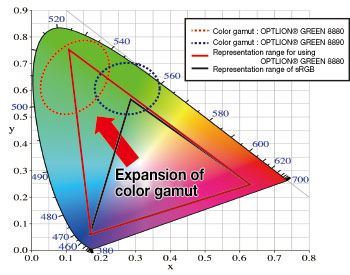
Inquiries
TOYO VISUAL SOLUTIONS CO., LTD.
TEL:+81-3-3272-3457