Ensuring Quality and Safety
Basic approach
artience group reliably implements quality assurance at all stages from planning and R&D to sales and after-sales service, and provides customers with products that can always be guaranteed. When developing new products and businesses, we evaluate and verify them in accordance with our own rules and commercialize them.
In addition, we utilize ISO 9001, an international standard for quality, to enhance and strengthen quality assurance throughout the Group.
In the medical field, such as transdermal patches, we produce products based on GMP (Good Manufacturing Practice), a standard for manufacturing and quality control of pharmaceuticals.
The artience Group (hereinafter referred to as the “Group”) aims to achieve customer peace of mind through the provision of safe products and services, and to earn the trust of customers through quality assurance with awareness of safety and security. To contribute to the sustainable growth of the Group and the improvement of social sustainability, we believe that it is necessary to continuously and progressively implement product safety and quality assurance activities. We have therefore established this Basic Policy on Product Safety and Quality Assurance (hereinafter referred to as this “Basic Policy”) and will engage in product safety and quality assurance activities at a high level.
- Scope of application
This Basic Policy applies to all products and services provided by the Group to its customers (including secondary materials such as containers and packaging, product accessories, products that the Group has been commissioned to manufacture by the third parties, products the manufacturing of which has been outsourced to third parties, products procured from third parties and provided to customers, prototypes, and samples; hereinafter referred to collectively as “products, etc.”) It also applies to product safety and quality assurance activities at all stages, from product planning, research and development to after-sales service.
- Definition of quality
In our Brand Promise, the Group promises its stakeholders that it will provide the value of trust through high quality. The definition of “quality” here includes not only the specifications, properties, characteristics, functions, and performance of products required by customers, but also safety and environmental friendliness leading to the reduction and elimination of risks in the handling of products, etc.
- Quality assurance system
Each of the Group’s operating companies will establish an organizational unit to implement product safety and quality assurance activities in relation to the products under their control. Each organizational unit will establish a quality assurance system in compliance with international standards relating to quality management, such as ISO 9001, and strive to continuously improve it. The department that oversees product safety and quality assurance at artience Co., Ltd. will oversee these organizational units at operating companies and establish and operate a Quality Management Committee, chaired by the officer in charge of quality assurance at artience Co., Ltd. Through this group-wide structure, we will share information and develop measures at the group-wide level, and implement appropriate product safety and quality assurance activities as a group.
- Providing accurate information
When supplying products, etc., to customers, the organizational units that promote product safety and quality assurance activities at the operating companies responsible for the products will provide accurate information on specifications, quality assurance, and handling methods, etc., for the products. In particular, if the product is a chemical substance, they will provide and display SDS (Safety Data Sheets) and product labels prepared in accordance with the relevant laws and regulations of the country or region where the product is supplied, and the Globally Harmonized System of Classification and Labeling of Chemicals (GHS.)
- Response in the event of a problem
In the event of an accident caused by a supplied product, etc., or a problem such as the distribution of defective products, the organizational unit that promotes product safety and quality assurance activities at the operating company responsible for the product will implement appropriate emergency measures, investigate the cause, and prevent recurrences based on laws and regulations relating to product liability (PL,) the contents of delivery specifications, etc., and internal rules. In particular, if it is anticipated that a risk to the quality or safety of a product, etc., will affect consumers and other downstream members of the supply chain, we will implement appropriate information disclosure and response activities to minimize the occurrence of risks.
- Education and awareness-raising
The organizational units that promote product safety and quality assurance activities at each operating company will continue to provide appropriate education and training regarding product safety and quality assurance relating to products for which the company is responsible, to employees and others engaged in work ranging from planning, research and development to after-sales service. In this way, we will endeavor to maintain and improve the level of product safety and quality assurance at each operating company.
- Revision, abolition and management
Decisions regarding the revision or abolition of this Basic Policy shall be made by the Board of Directors of artience Co., Ltd.
The department in charge of the revision and abolition of this Basic Policy shall be the department that oversees the product safety and quality assurance of artience Co., Ltd.
Established on May 10, 2024 (resolved at the Board of Directors on May 10, 2024)
Promotion system
Led by the Quality Management Committee, we carry out activities aimed at building a quality assurance system and improving the level of quality assurance at all of our group's production bases. At the semi-annual Quality Management Committee, we aim to share quality improvement activity strategies at all domestic and overseas production sites.
In addition, to ensure that customers can use our group's products with peace of mind, Production-Logistics Planning Department artience Co., Ltd. holds a "quality risk diagnosis meeting" to check the situation at each site from a third-party perspective and We are promoting the creation of a corporate culture that prevents fraud.
In addition, in order to further stabilize quality and reduce quality risks, we have established the "Global Standard for Quality," a quality standard that will enable us to supply the same high-quality products anywhere in the world, and will roll it out to all production sites. We are proceeding.
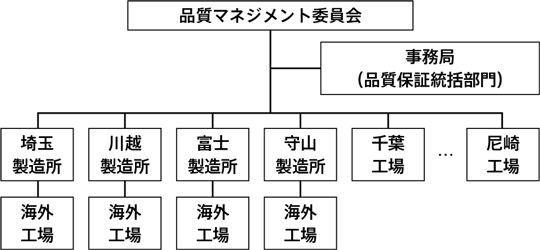
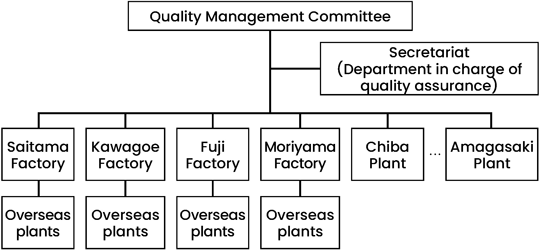
attempt
Management and provision of product information
In addition to distributing SDS (Safety Data Sheets) of its products to customers by employees, the Group also provides them through the Company's customer portal site "Sommelier." We have built a system to provide product information more quickly and support our customers. In the event of a serious product accident, we have established a risk management system to ascertain the facts and identify the scope of the impact in accordance with internal regulations, promptly report the situation to management, report to the competent authorities in accordance with laws and regulations, disclose information through our website, etc., and take prompt and appropriate measures.
In addition to our own products, we also sell products of other companies (products for sale), and we strive to handle and manage our products in consideration of the safety of our customers.
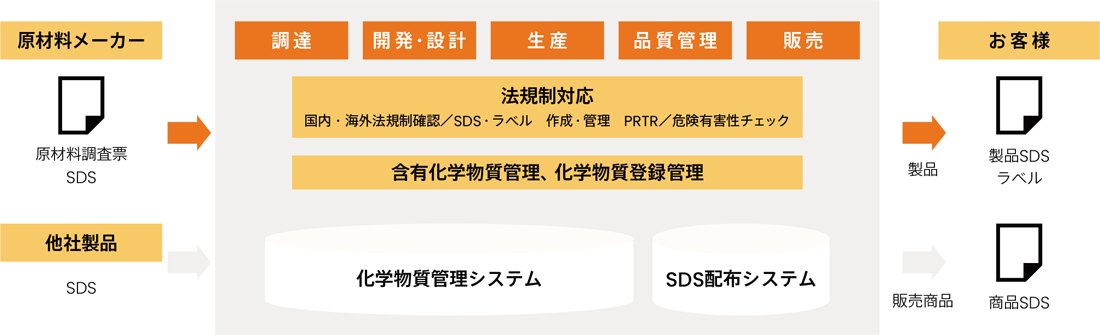
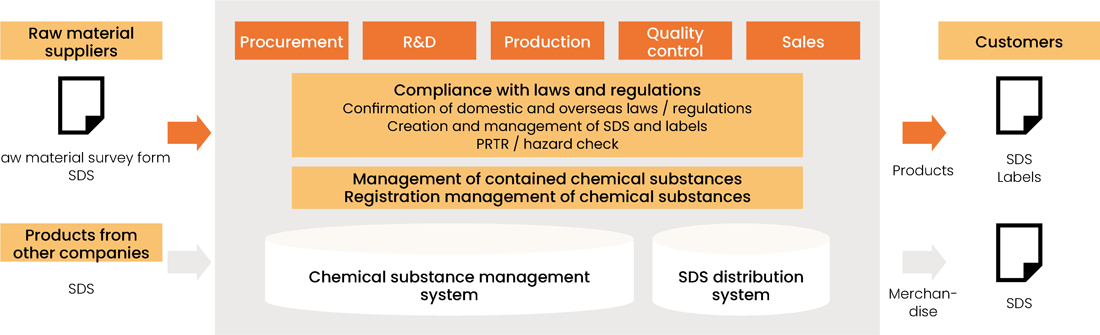
Number of serious product accidents
(Unit: cases)
2021 | 2022 | 2023 | |
---|---|---|---|
Number of serious product accidents | 0 | 0 | 0 |
Providing product safety information globally and complying with laws and regulations
In order to provide global information to customers in each country, our group is equipped with an SDS creation system that supports the languages and laws of export destinations, and is unique in that it can centrally manage information on chemical substance-related laws and regulations in each country and region. We operate a chemical substance management system. Group companies in Japan and overseas are promoting the operation of this system and supporting customers' risk assessments by providing SDS that comply with the laws and regulations of each country. Furthermore, in order to properly comply with the information stipulated by each country's laws and regulations on labels, the GHS guidelines are used as a group standard at each domestic and overseas group company.
Even at our overseas bases, we are working to strengthen compliance with chemical substance-related laws and regulations by promoting the use of search tools that allow us to check whether a chemical substance name falls under each country's laws and regulations.
In order to provide global information on product safety to customers in each country, the Group is equipped with a safety data sheet (SDS) preparation system that corresponds to the languages and laws and regulations of the export destination, and operates a unique chemical substance management system that can centrally manage information on chemical substance-related laws and regulations in each country and region. Group companies in Japan and overseas are operating this system to support customers' product safety risk assessments by providing product labels that comply with SDS and GHS-compliant "Label Guidelines" that comply with the laws and regulations of each country.
In December 2023, in addition to complying with existing laws and regulations, we updated the specifications of the Chemical Substance Management System with the aim of further strengthening consideration for environmental conservation and restoration and the health, safety, and security of people. This specification change will further improve the labeling of hazard information, etc. in SDS and product labels for Japan.
Responding to product risk information
Our group has established ``Product Risk Information Response Guidelines'' in order to promptly and appropriately respond company-wide to product risks. Production-Logistics Planning Department artience Co., Ltd. and other organizations work together with core operating companies and affiliated companies to address product risks as part of quality assurance activities.