Occupational Safety and Health, Process Safety and Disaster Prevention
Basic approach
In its Basic Policy on Occupational Health and Safety (revised in January 2024), artience group states that "in order to sustainably improve occupational health and safety in the workplace, we will strive for safe operations, safety and disaster prevention, and hygiene management based on the premise of compliance with laws and regulations and respect for international norms," and we will do our utmost to prevent accidents and take safety measures for buildings and facilities. In addition, in order to ensure a high level of the Basic Policy on Occupational Health and Safety, which is the basis of safety, we have established an occupational health and safety management system at each business site that is tailored to the content of each business activity, and we are actively engaged in safety and health activities based on risk management.
The artience Group (hereinafter referred to as the “Group”) has established a mission of “building a future where all people can live enriched lives” through its corporate activities in manufacturing. We believe that the Group’s role as a corporate citizen, and as a chemical manufacturing company, can be fulfilled by ensuring the safety and health of all Group employees.
Based on this basic approach, we have established this Basic Policy on Occupational Safety and Health (hereinafter referred to as this “Basic Policy”). To sustainably improve occupational safety and health in the workplace, we will endeavor to engage in safe operation, safety and disaster prevention, and hygiene management based on the assumption of compliance with laws and regulations and respect for international norms.
- Scope of application
This Basic Policy applies to all companies and organizations that make up the Group. In addition, all officers, corporate advisors, employees, contract employees, and part-time employees of the Group, as well as temporary dispatch workers and all other persons engaged in the Group’s business operations (hereinafter referred to collectively as “officers and employees”) are obligated to comply with this Basic Policy. We also ask all suppliers, distributors, and other business partners who form the Group’s supply chain to understand and support this Basic Policy. - Building and operating an occupational safety and health system
The Group will establish and operate a Group-wide management system for the purpose of ensuring and improving workplace safety and the health of officers and employees. We will establish an occupational health and safety management system at each business site that is tailored to the content of each site’s business activities, and we create a network that links these systems. Through the operation and continuous improvement of this company-wide system, we will share information, set goals and implement measures, and work to reduce and avoid all occupational safety and health risks within the Group. - Management of occupational safety and health risks
The Group will find, evaluate, and identify a variety of occupational safety and health risks at its production sites and sites that engage in non-production business activities. In addition, we will engage in appropriate management to reduce these risks, eliminate hazards that are risk factors, limit the possibility of risk manifestation, or minimize the damage suffered by workers when risks occur. - Improvement of safety and health environments in the workplace
The Group will ensure the safety and health of officers and employees in the course of their duties by using appropriate equipment, technical measures, and management methods, according to the nature of each workplace. Specifically, we will provide personal protective equipment free of charge, introduce ventilation and air conditioning equipment, keep medical equipment and supplies on hand, improve working environments for physically demanding work, and make reasonable accommodations for female workers during pregnancy and nursing (breastfeeding.) - Preparations against occupational accidents and illnesses
The Group will ascertain the state of occurrence of occupational accidents and illnesses, provide necessary treatment, record cases, investigate and analyze causes, and take appropriate corrective measures to eliminate them, with the aim of minimizing and preventing repeat occurrences of occupational accidents and illnesses. We will also work to create a workplace environment and systems that support workers who have been affected by occupational accidents or illnesses when they return to work. - Emergency response
The Group will place the highest priority on the lives and physical and mental safety of its officers and employees, and will prepare appropriate emergency response and recovery measures in advance, based on specific assumptions of disasters and accidents that may occur, regardless of the number of occurrences. To improve the effectiveness of these measures, we will inform officers and employees of evacuation routes, etc., and conduct evacuation drills at a level of frequency that exceeds legal standards. - Worker health management
The Group will provide appropriate health management for all officers and employees. We will conduct regular health checks for officers and employees in accordance with relevant laws and regulations. In particular, we will conduct necessary examinations for workers engaged in specific work duties, such as the handling of chemical substances. We will also work to improve health management throughout the Group, such as by preventing health problems caused by overwork and exposure to chemical substances, and promoting mental health care. At the same time, all officers and employees will endeavor to manage their own health, in order to maintain sufficient health in the performance of their duties. - Information disclosure and dialogue
The Group will disclosure information on occupational safety and health both internally and externally, and engage in active communication, including the clarification and sharing of health and safety information among officers and employees. In particular, we will encourage employees to report occupational accidents and illnesses and raise concerns about safety and health in the workplace, and work to create a workplace environment where everyone can express their opinions and engage in dialogue without hesitation. - Enlightenment, education, and training
The Group will distribute this basic policy and various information relating to occupational safety and health, and will continue to provide appropriate awareness-raising, education, and training, to ensure that all officers and employees understand the importance of maintaining and improving occupational safety and health, acquire the correct knowledge and skills, and develop the ability to detect potential risks and respond to them in a way that leads to risk reductions. - Revision, abolition and management
Decisions regarding the revision or abolition of this Basic Policy shall be made by the Board of Directors of artience Co., Ltd.
The department in charge of the revision and abolition of this Basic Policy shall be the department that oversees occupational safety and health activities at artience Co., Ltd.
Established in June 1996
Revised on January 1, 2024 (Resolved at Board of Directors on December 8, 2023)
PDF[日本語・英語・簡体字中国語・繁体字中国語・韓国語・マレー語・ベトナム語・フィリピノ語・インドネシア語・フランス語・ポルトガル語(ブラジル)・ハンガリー語]
Promotion system
artience Production-Logistics Planning Department Co., Ltd. is responsible for promoting the prevention and recurrence of occupational accidents and disaster prevention accidents by conducting audits, risk assessments, accident investigations, and confirmations related to the prevention of occupational accidents and safety and disaster prevention accidents for the entire Group, and by providing important information on occupational safety and health and instructing the Group as a whole to take appropriate measures globally through the Safety Network Meetings in Japan and overseas.
In addition, in order to prevent occupational accidents and safety and disaster prevention accidents and prevent their recurrence, we regularly conduct safety education and distribute a monthly "Past Accident Review Calendar" in Japan and overseas, which summarizes occupational accidents and safety and disaster prevention accidents that have occurred within the Group in the past, to raise safety awareness and improve skills throughout the Group through sharing and discussing examples of safety initiatives related to past accidents.
In response to natural disasters such as large-scale earthquakes, fires, and accidents, we work with Risk Management Committee to consider measures to prevent disasters and accidents and minimize damage, and to establish an emergency contact network.
We regularly hold management council meetings to discuss issues with the labor union and the company, and strive to improve work styles, including safety and health. In addition, the Safety and Health Committee, which consists of managers, managers, and labor union members, meets every month at each site to report and discuss occupational health and safety, including occupational accidents. The minutes of committee meetings are posted on the company intranet and other means to disseminate them to employees.
(FY2024)
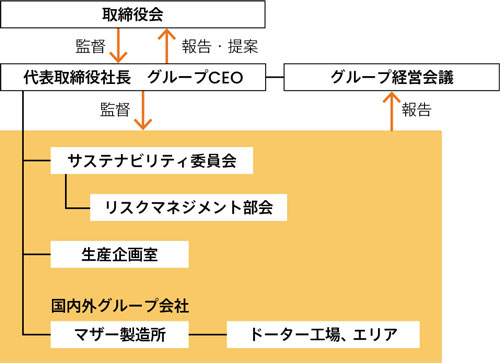
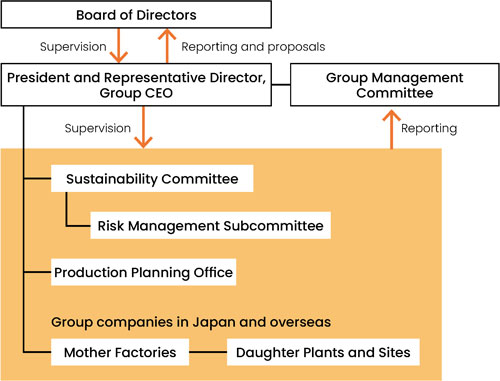
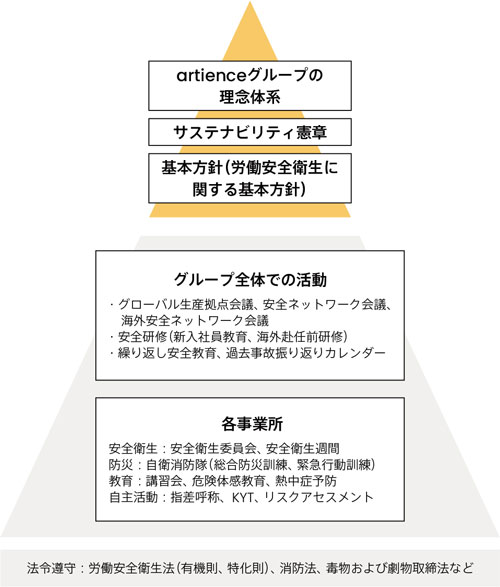
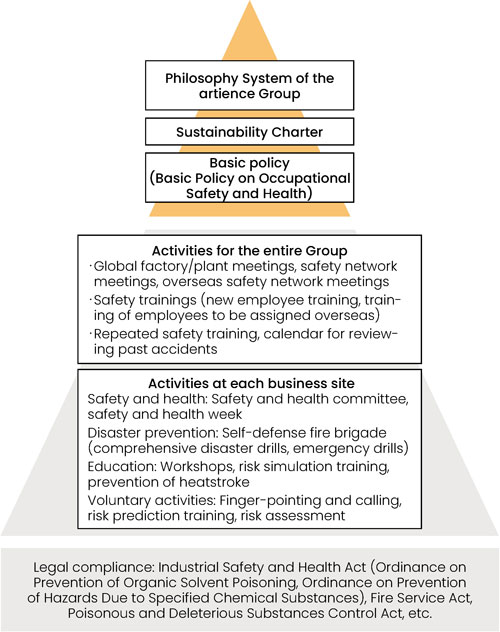
attempt
Frequency rate/severity rate
In the Group (domestic and in-house), the frequency rate of lost-time injuries increased due to an increase of one accident from 2022. On the other hand, the intensity rate increased due to the increase in the number of days off work by 13 days.
As a result, the frequency rate was 0.438 and the intensity rate was 0.003, which was lower than that of the manufacturing and chemical industries as a whole. The Group is working to prevent recurrence by clarifying the causes of accidents, including lost-time accidents, and countermeasures.
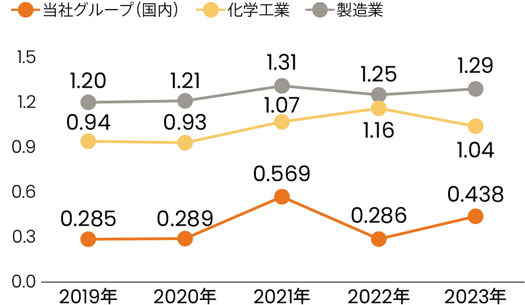
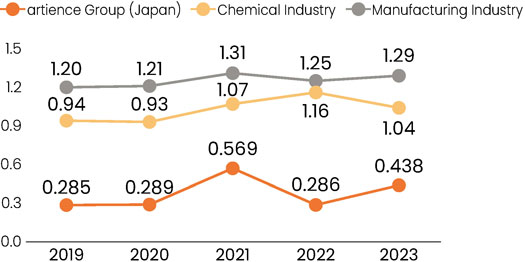
* 1 External data showing the frequency of lost-time accidents in terms of the number of lost-time accidents per 1 million total actual working hours is quoted from the Ministry of Health, Labour and Welfare's "Overview of the Reiwa 5-Year Survey on Trends in Occupational Accidents (Survey of Business Establishments)."
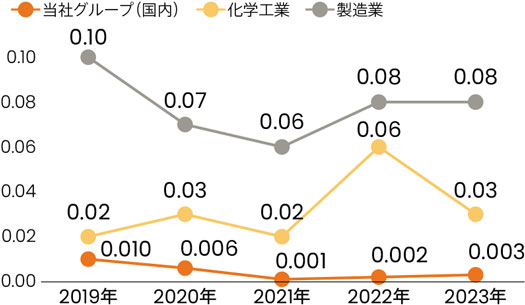

* 2 External data showing the severity of lost-time injuries in terms of the number of days lost per 1,000 total actual working hours is quoted from the Ministry of Health, Labour and Welfare's "Summary of the Reiwa 5-Year Survey on Trends in Occupational Accidents (Survey of Business Sites)."
(Unit: cases)
2019 | 2020 | 2021 | 2022 | 2023 | |
---|---|---|---|---|---|
The Group (Domestic, in-house *) |
2 | 2 | 4 | 2 | 3 |
* In-house: Employees at all of the Group's domestic offices (including contract employees, part-time workers, and temporary employees)
- Hazard identification, risk assessment, accident investigation
- Training on occupational safety and health
- Domestic and international network conferences
- Safety and disaster prevention initiatives